Preparing STL files
Rapid prototyping printing machines work with STL (stereolithoghaphy) files. STL models are polygon mesh object formed of small flat facets. Curved surfaces contain large number of these vary small flat facets and to the human eye they appear curved.
When we make models with a 3D program as Catia, Solidworks or Rhinoceros we work with IGES or NURBS surfaces. These surfaces are defined mathematically, therefore the curves are perfect. When we treansform these curved surfaces in faceted surfaces we need to indicate to the program which type of quality we want to apply. Rhinoceros is one of the most versatile programs regarding this issue and since we can control all the factors that define the quality of STL.
Smaller models as jewelry pieces need greater definition than bigger models. Parameters we usually use are these:
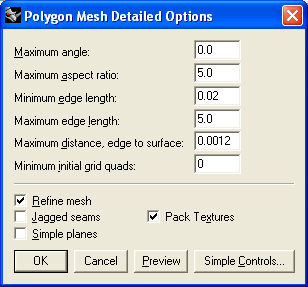
Maximum aspect ratio (5.0): this value represents the tolerance between two edges of the square. If one edge is 1 the other will be maximum 5. Normaly, 3D printers require values near to square.
Minimum edge length: STL faces of 3 or 4 sides will have at least a distance of 0.02 mm. Large number of lines smaller than 0.02 mm would increase file size and could cause triangulation problems.
Maximum edge length: We reccomend that maximum edge lenght of the facet be 5 mm.
Maximum distance, edge to surface: This value is very important: defines the quality of STL by specifying the distance of facets from the modelled surface. Smaller the distance means that mesh definition is higher. We reccomend the value between 0.0015 and 0.0012 mm as smaller values would only produce extra information that prototyping machine can not use.
Values that equal 0 are not calculated by Rhinoceros. We recommend activating the "Refine mesh" checkbox.
|